Polyurethane spray conduction is an innovative assembling process that includes the utilization of blended gas (hydrogen peroxide) to uncover strong materials (like plastic, wood, and so forth.) to ultra-violet light.
The subsequent "regurgitate" of the SPRAY procedure scatters the stored SPRAY into the material and keeps it in an express that permits it to dry. Drying time is reliant on the heaviness of the SPRAY, the thickness of the SPRAY and the length of presentation to the light. The outcome is a variety of plastic dots that are exceptionally adaptable, permitting the makers to include (or expel) distinctive SPRAY components as indicated by the structure specifications of the item.
Polymer coatings are utilized for a wide scope of applications. The producer can apply a plastic sap to the outside surface of wood, vinyl or aluminum items to improve their toughness. The items can be furnished with (or without) polymers for different commonsense reasons: Additional info found at CONTAINMENT COATING.
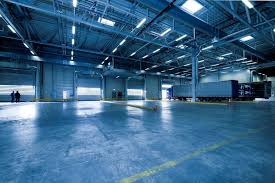
They can help make a progressively appealing look to your items. Moreover, the polymers offer unique UV stabilizers, UV protection and climate obstruction. They help seal the item from dust, water, soil and oil.
In addition, polymers offer inside turn throwing and extrusion abilities for mechanical purposes. In this manner, the maker can without much of a stretch change the sort of SPRAY required for the particular application.
Polyurethane spray conduction is additionally used to deliver reflexive surfaces on vinyl, hardened steel and plastics. Since they have explicit properties like (or far and away superior to) traditional paints, polyurethane coatings can be applied to secure against heat presentation, make the surface more scratch-safe and increment the shininess of the item.
The latest improvements of polyurethane spray-cast items are amazingly proficient at securing against warmth and UV-radiation, leaving the item for all intents and purposes imperceptible and for all intents and purposes without scratch. Along these lines, the SPRAY formulations are broadly utilized for modern applications, for example, warm expansion machines, friction stirrers, vacuum siphons, water purification, cleaning hardware, cooling frameworks, and even clinical gadgets.
Polymer coatings are as yet being utilized in various other modern applications, for example, cleaning, bonding, getting done with, painting, mechanical and car parts. What's more, a lot more application zones are yet to be investigated.
The subsequent "regurgitate" of the SPRAY procedure scatters the stored SPRAY into the material and keeps it in an express that permits it to dry. Drying time is reliant on the heaviness of the SPRAY, the thickness of the SPRAY and the length of presentation to the light. The outcome is a variety of plastic dots that are exceptionally adaptable, permitting the makers to include (or expel) distinctive SPRAY components as indicated by the structure specifications of the item.
Polymer coatings are utilized for a wide scope of applications. The producer can apply a plastic sap to the outside surface of wood, vinyl or aluminum items to improve their toughness. The items can be furnished with (or without) polymers for different commonsense reasons: Additional info found at CONTAINMENT COATING.
They can help make a progressively appealing look to your items. Moreover, the polymers offer unique UV stabilizers, UV protection and climate obstruction. They help seal the item from dust, water, soil and oil.
In addition, polymers offer inside turn throwing and extrusion abilities for mechanical purposes. In this manner, the maker can without much of a stretch change the sort of SPRAY required for the particular application.
Polyurethane spray conduction is additionally used to deliver reflexive surfaces on vinyl, hardened steel and plastics. Since they have explicit properties like (or far and away superior to) traditional paints, polyurethane coatings can be applied to secure against heat presentation, make the surface more scratch-safe and increment the shininess of the item.
The latest improvements of polyurethane spray-cast items are amazingly proficient at securing against warmth and UV-radiation, leaving the item for all intents and purposes imperceptible and for all intents and purposes without scratch. Along these lines, the SPRAY formulations are broadly utilized for modern applications, for example, warm expansion machines, friction stirrers, vacuum siphons, water purification, cleaning hardware, cooling frameworks, and even clinical gadgets.
Polymer coatings are as yet being utilized in various other modern applications, for example, cleaning, bonding, getting done with, painting, mechanical and car parts. What's more, a lot more application zones are yet to be investigated.
No comments:
Post a Comment